Plastic PE bottles are widely used in various industries for packaging liquids and other substances. Understanding the manufacturing process behind these bottles provides valuable insights into the steps involved in transforming raw materials into the final product.
Material Selection and Preparation:The first step in the manufacturing process is selecting the appropriate grade of polyethylene (PE) resin. High-density polyethylene (HDPE) and low-density polyethylene (LDPE) are commonly used for plastic bottle production. The resin is carefully chosen based on factors such as desired bottle properties, end-use requirements, and regulatory compliance. The selected resin is then prepared for the subsequent processing steps.
Extrusion:Extrusion is a primary method used to shape plastic PE bottles. In this step, the resin is heated and melted, forming a molten plastic mass. The molten plastic is then forced through a die, which imparts the desired shape and size to the bottle. The extruded tube is continuously cooled and solidified to maintain its shape.
Bottle Formation:Once the extrusion process is complete, the extruded tube is cut into individual sections, commonly referred to as "parison" or "preforms." These preforms resemble miniature bottles and serve as the starting point for the final bottle formation.
Injection Stretch Blow Molding:Injection stretch blow molding is a widely used technique to produce plastic PE bottles. The preforms are heated to a specific temperature and then loaded into a blow molding machine. The machine clamps the preform and stretches it axially while injecting high-pressure air into it. The air expands the preform, conforming it to the shape of the mold cavity. The mold is cooled, allowing the bottle to solidify and retain its shape.
Trimming and Deflashing:After the blow molding process, excess material, known as flash, may be present on the bottle. Trimming and deflashing operations remove this excess material and ensure the bottles have clean, smooth edges.
Printing and Labeling (Optional):Depending on the intended use and branding requirements, plastic PE bottles may undergo printing or labeling processes. These processes apply necessary information, such as product details, logos, barcodes, or regulatory markings, onto the bottles.
Packaging and Distribution:The final step involves packaging the plastic PE bottles in suitable containers, such as boxes or pallets, for storage and transportation. Proper packaging ensures protection during handling and transportation, maintaining the quality of the finished bottles until they reach their intended destination.
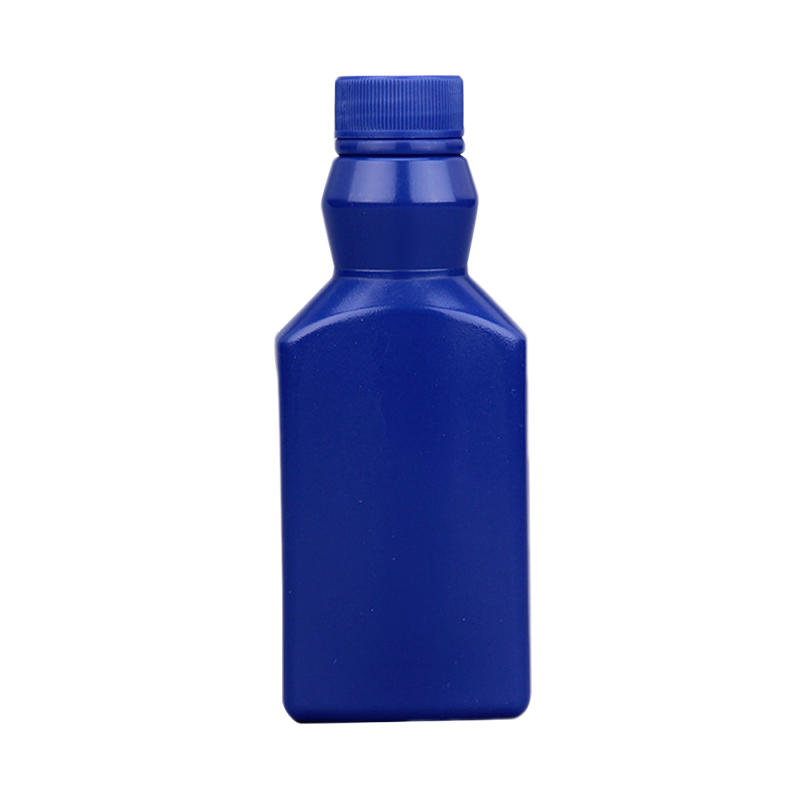
Number PE-004
Capacity (ml) 120
Diameter (mm) 51×34
Self weight(g) 18